ПНИПУ запатентовал состав керамических форм для литья деталей самолетов
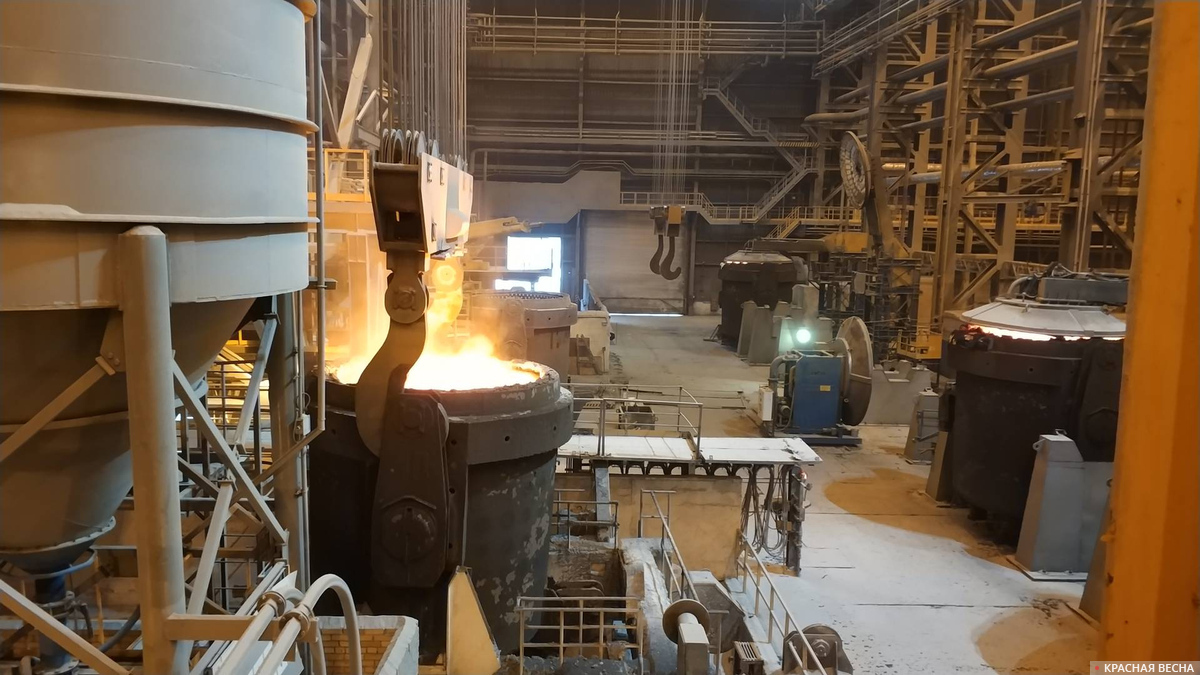
Состав и технологию изготовления литейных керамических форм, позволяющие снизить их себестоимость, разработали и запатентовали ученые Пермского национального исследовательского политехнического университета (ПНИПУ), 8 июня сообщает пресс-служба вуза.
Литые детали находят широкое применение при конструировании самолетов. Литьем можно изготавливать при минимальной механической обработке корпусные детали, фитинги, качалки, кронштейны, фланцы, ручки и другие детали.
Более экологичный и технологичный метод, разработанный специалистами Пермского Политеха, позволяет одновременно улучшить качество продукта, экономить средства предприятий и решать проблему утилизации отходов.
Разработчики нового состава для керамических форм поясняют, что в широко применяемый в настоящее время состав для литейных форм входит большое количество регулирующих добавок, что увеличивает стоимость продукта.
Предложенный политехниками для изготовления литейных форм струвит, который получают в результате очистки хозбытовых и производственных стоков, плюс коллоидный кремнегель из гидросиликата магния позволят значительно снизить себестоимость форм. При этом новый материал пожароустойчив и экологически безопасен.
Доцент кафедры «Химические технологии» ПНИПУ кандидат технических наук Андрей Старостин рассказал о разработанном ими материале:
«Использование струвита для изготовления литейных форм, полученного из промышленных отходов, в качестве сырья вместо огнеупорного наполнителя и магнийсиликатного порошка позволяет снизить себестоимость получаемого состава. Использование в качестве связующего коллоидного кремнегеля из гидросиликата магния с влажностью 41–50% обеспечивает необходимую пластичность указанного состава и высокую прочность получаемых керамических форм».
Ученые провели исследование нового состава литейных форм. Они смешивали струвит с кремнегелем до образования пластичной массы и ею заполняли фторопластовые формы (матрицы). Затем образцы в течение 24 часов подвергались сушке при температуре 25 °C и еще 1 час в сушильном шкафу при температуре 200 °C. Полученные образцы проверялись на прочность и сжатие.
Тестирование показало, что новый состав обладает высокими прочностными свойствами и может быть рекомендован для изготовления керамических форм для высокоточного литья.
Еще одним достоинством новой технологии при ее внедрении является возможность переработки отходов.
Разработкой ученых Пермского Политеха заинтересовались в конструкторском бюро АО «ОДК-Авиадвигатель».