Ученые разработали метод высококачественной лазерной полировки деталей
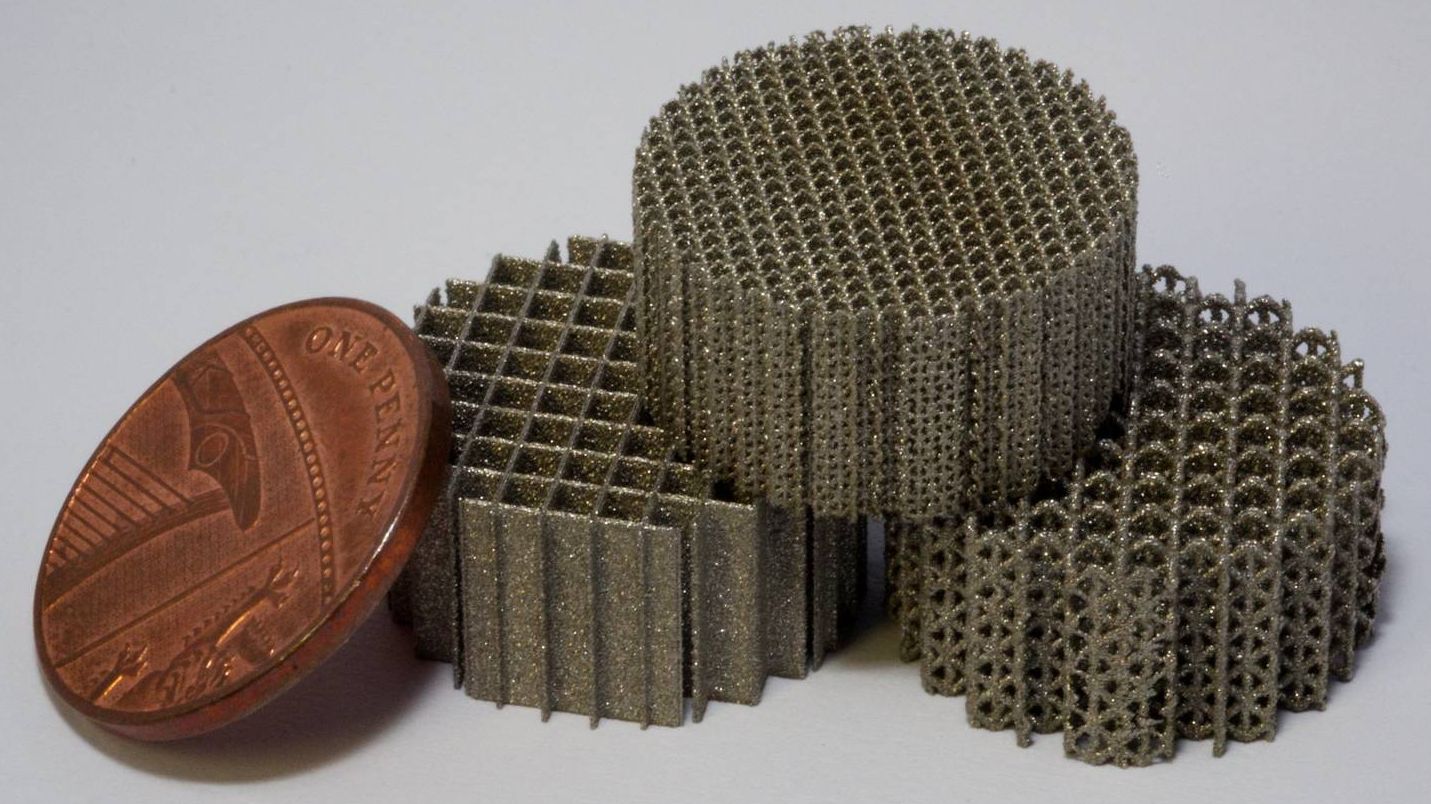
Эффективный метод лазерной полировки металлических деталей сложной формы, изготовленных на 3D-принтере, разработали ученые Сколковского института науки и технологий и Национального исследовательского ядерного университета МИФИ, сообщает 7 сентября пресс-служба Сколтеха.
Разработчики предлагают использовать новую технологию для полировки и устранения лазером глубоких пор при изготовлении на 3D-принтере металлических протезов суставов.
Результаты исследования новой технологии ученые представили в статье «Эффект заживления пор при лазерной полировке и его влияние на усталостные свойства деталей из нержавеющей стали 316L, изготовленных методом лазерной плавки в порошковом слое», опубликованной в журнале Optics & Laser Technology.
Достоинствами нового метода является устранение глубоких пор, которые образуются при изготовлении деталей методом спекания металлического порошка на 3D-принтере, при этом одновременно с полировкой происходит уплотнение подповерхностного слоя и повышение усталостной прочности и плотность металла под поверхностью.
Другие существующие в настоящее время методы обработки поверхности на это неспособны. Стандартная лазерная полировка хорошо полирует деталь, но не может справиться с подповерхностными порами, образующимися при спекании лазером металлического порошка во время изготовления детали на 3D-принтере.
Первый автор статьи, аспирант Центра технологий материалов Сколтеха Даниил Панов пояснил: «На 3D-принтере можно изготовить металлические детали весьма сложной формы, но их поверхность получается шероховатой, а на глубине порядка 0,1 мм формируются дефекты в виде пор. Наш коллектив модифицировал традиционную технологию лазерной полировки таким образом, что она стала снижать примерно на порядок и шероховатость поверхности, и пористость приповерхностного слоя».
Он уточнил, что они проверяли свою технологию на стальных образцах, но аналогичные результаты вполне достижимы с такими распространенными материалами для протезов, как титан и сплав кобальта с хромом.
Панов рассказал: «Наша идея проста: вместо нескольких проходов лазером по поверхности на „оптимальной“ мощности, как это обычно делается, повысить мощность одного из проходов, чтобы расплавить более толстый слой металла и достать до пор. Конечно, оптимальной эту мощность называют не просто так, поэтому поверхность в итоге получится чуть более шероховатой, но речь об очень незначительном ухудшении, в пределах нескольких процентов, зато взамен мы избавляемся от вредных дефектов под поверхностью».
Альтернативой могла бы стать фрезеровка — механическое удаление верхнего слоя материала толщиной примерно 0,2 мм, которая удалит приповерхностные поры и поверхность обработки будет гладкой. Однако она не подходит для сложных по форме деталей — таких, какие обычно изготавливают с помощью 3D-печати, отмечают авторы разработки.
«Мы дополнительно исследовали, как наш подход к полировке отражается на усталости металла, — добавил Панов. — Это свойство наряду с шероховатостью и приповерхностными дефектами имеет значение для медицинских протезов, поскольку они подвергаются циклическим механическим нагрузкам. Так вот, оказалось, что вдобавок к снижению шероховатости и пористости примерно на 90% мы получаем ещё и улучшение с точки зрения выносливости металла».
Важность борьбы с приповерхностными дефектами в том, что у детали, которая подвергается циклическим нагрузкам и постепенному стиранию, как, например, искусственный сустав, залегающие под поверхностью поры со временем обнажаются и становятся очагами ускоренного разрушения материала, отметил Панов.
Он добавил, что «лазерная полировка хороша тем, что ее можно применять очень точечно: скажем, искусственный коленный сустав имеет сложную форму, и там есть участки поверхности, которые не нужно полировать, где шероховатость, наоборот, помогает интеграции с биологической тканью».
На перспективы нового метода для структурирования поверхностей обратил внимание руководитель исследования, доцент Центра технологий материалов Сколтеха Игорь Шишковский:
«Изменение маслоемкости поверхности, условий смачивания и тривиальная гравировка давно у всех на слуху. Но есть и более сложные, но выполнимые задачи — например, структурирование поверхности импланта перед хирургической операцией, создание специальных меток для идентификации, формирование на поверхности дифракционных решёток для диагностики функциональных изделий».