Ученые создали технологию 3D-печати из жаропрочных титановых сплавов
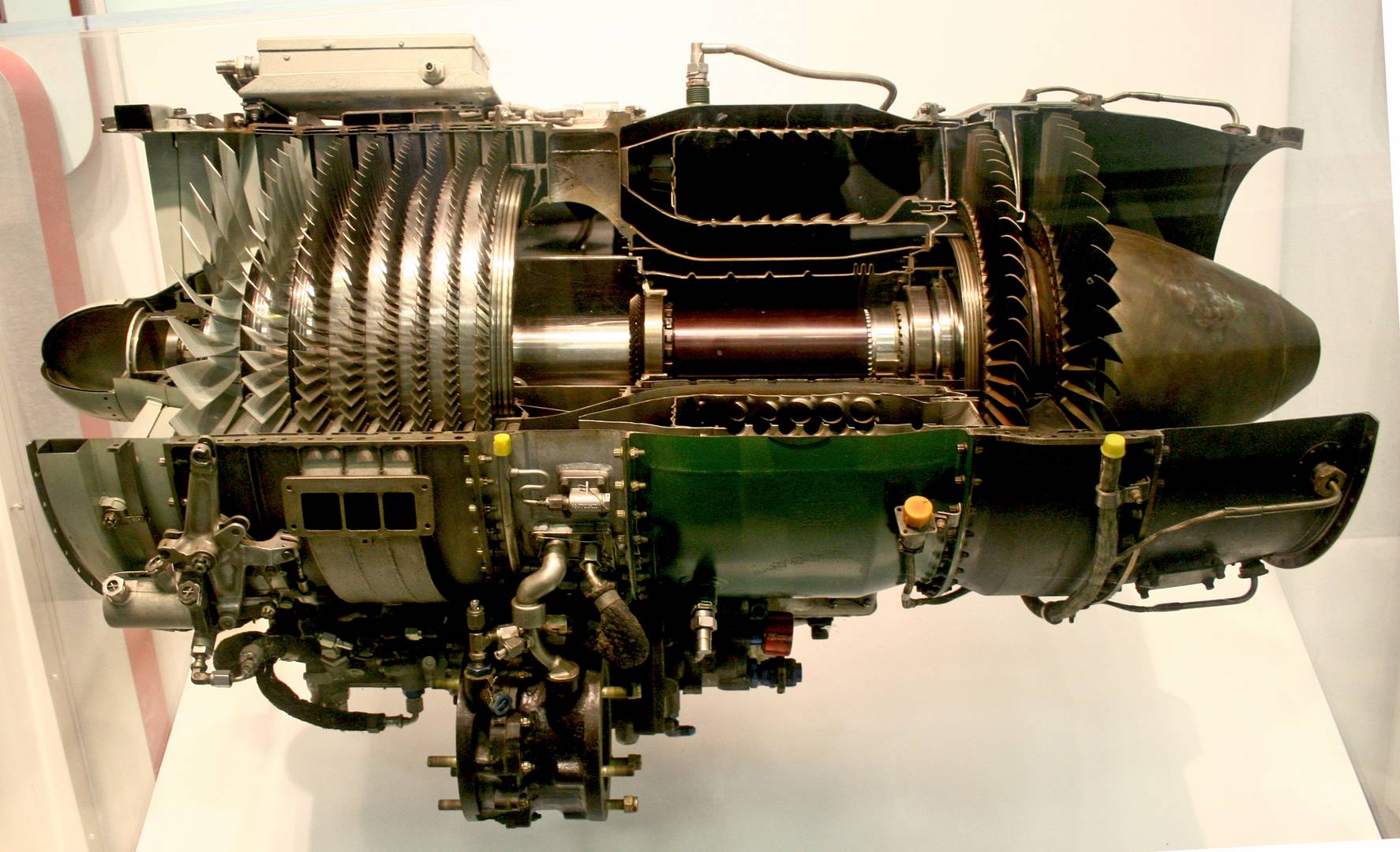
Технологию формования жаропрочных сплавов из порошка на основе алюминидов титана для изготовления газотурбинных двигателей в авиационно-космической отрасли разработала команда ученых из Уральского федерального университета (УрФУ) и Индийского института науки в Бангалоре, 22 октября сообщает пресс-служба УрФУ.
Соавтор работы, доцент кафедры термообработки и физики металлов УрФУ Степан Степанов пояснил преимущества алюминидов титана:
«Снижение веса изделий для авиационно-космической техники решит ряд задач: повысит экономичность, снизит вес, увеличит грузоподъемность летательных аппаратов. Одним из решений этих задач может стать использование в деталях двигателя и других компонентах жаропрочных сплавов на основе алюминидов титана. Изделия из таких сплавов крайне прочные, выдерживают температуры до 700 ℃ и легче аналогов из железа и никеля».
В настоящее время детали из алюминидов титана создают по традиционным технологиям из деформированных полуфабрикатов, прутков и тому подобное. Такая технология, состоящая из нескольких этапов, достаточно затратна. Она включает в себя получение заготовки, ее механическую обработку и последующую термическую обработку.
Однако интерметаллиды (химическое соединение двух или более металлов), к которым относятся алюминиды титана, обладают низкой пластичностью, что затрудняет изготовление из них сложных деталей при помощи более простой технологии, такой как обработка давлением. Решением проблемы выбора более оптимальной технологии изготовления деталей из данного сплава посвятила свое исследование команда российских и индийских ученых.
Они решили заменить традиционный способ обработки аддитивным (печатью образцов из порошка на 3D-принтере). Порошок алюминида титана для них под заказ создал российский производитель. Печать образцов выполнялась также на отечественном 3D-принтере.
Новая технология изготовления детали из алюминида титана требует меньше времени, так как состоит из одной операции — сплавления тонкого слоя порошка лазером, многократный повтор которой позволяет вырастить из нескольких таких слоев изделие практически любой сложной формы с точными размерами, не требующими дополнительной подгонки.
«Нам предстояло решить ряд задач, в частности, улучшить механические и эксплуатационные свойства изделий: снизить количество пор, непроплавов, химическую неоднородность, повысить пластичность, избежать мелких трещинок и так далее», — рассказал Степан Степанов о проведенных исследованиях.
Подобрав в ходе экспериментов оптимальные технологические параметры 3D-печати, термической обработки, состава сплава и решив некоторые другие проблемы, ученые добились получения заданной структуры материала и отсутствия в ней дефектов.
«В общем, нам удалось создать технологию и получать изделия методом, который раньше в принципе не использовали для таких материалов», — отметил Степан Степанов.
Характеристики получаемых из алюминида титана изделий ученые представили в статье «Влияние технологических параметров селективного лазерного плавления на структуру, текстуру и механические свойства сплава на основе орторомбического алюминида титана Ti₂AlNb» (Effect of process parameters of selective laser melting on the structure, texture, and mechanical properties of an alloy based on orthorhombic titanium aluminide Ti₂AlNb), опубликованной в журнале Metallurgist.
Результаты проведенных испытаний показали, что новая технология находится на уровне мировых разработок в материаловедении. В планах научной команды адаптировать ее для промышленного внедрения и исследовать возможности применения аддитивной технологии для других сплавов.